
Slow and Steady: Shibori Resist Dyeing with Indigo
Patience is a virtue, but it’s certainly not one that I possess. I’m not exactly the best at waiting (is it just me or is thirty seconds way too long to wait for pizza to microwave?), so the idea of waiting a year for something sounds nearly torturous. The artisans working with our fair trade partners MESH and Manushi, however, are crafting beautiful textile designs using indigo dye that takes about a year to produce and proving that good things do indeed come to those who wait (if the taste of that cold-in-the-center leftover pizza wasn’t enough of an indication).
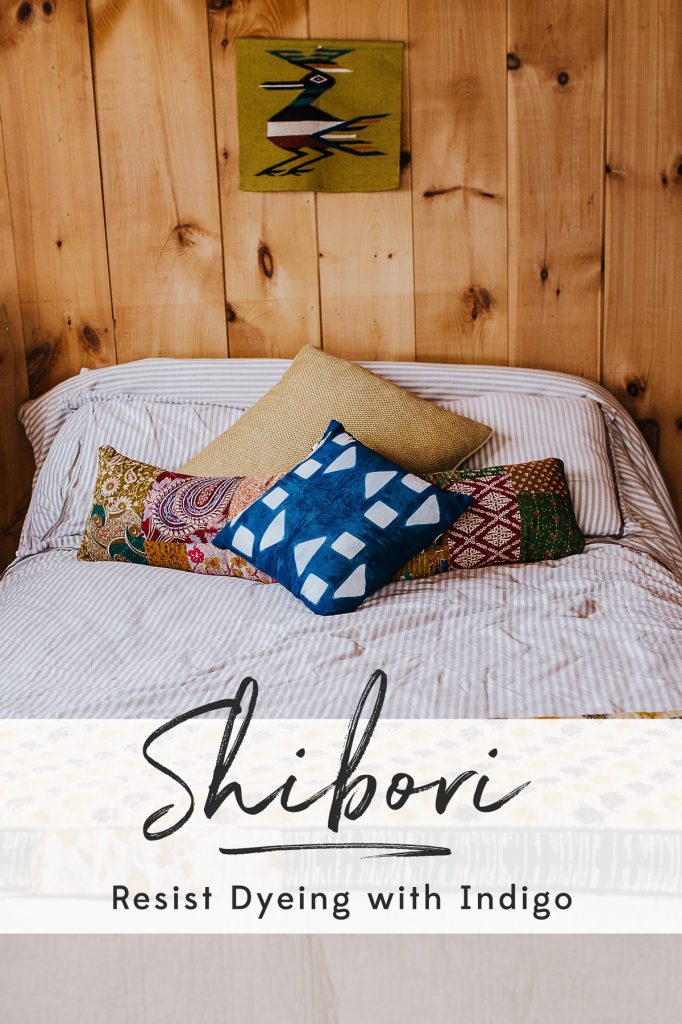
Indigo is made by harvesting leaves from an indigofera plant and drying them in the sun. The leaves are flipped repeatedly with a broom until they turn blue.
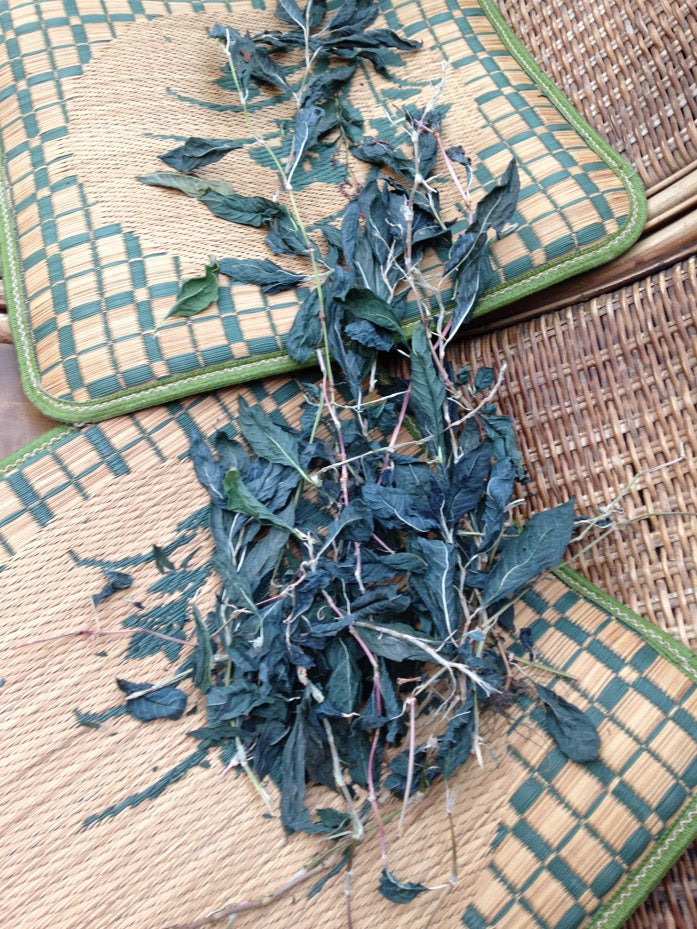
Indigo is a gorgeous color, but if your patience meter is anything like mine, you’re probably still wondering why anyone would spend nearly a year trying to produce indigo ink. Surely, there are other blues we can make in half the time, right? Technically, yes, but looks aren’t everything!
Natural indigo has some superpowers in addition to its beautiful color.
Samurais wore fabric dyed in indigo under their armor, utilizing its antibacterial qualities to protect wounds. Indigo was also once used in Japanese firefighters clothing because it is known to be flame resistant, but don’t test this at home (seriously, our indigo-dyed fabrics are cotton and will burn, so don’t even think about it).
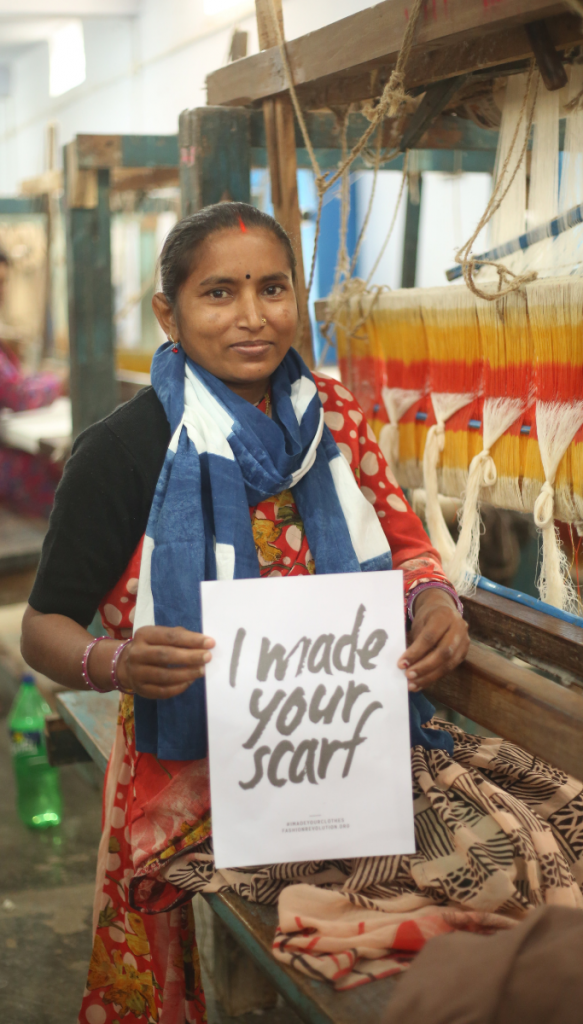
To create the Indigo Geo Print Pillows and Shibori Scarf, MESH works with a dyeing workshop called Little Flower in northern India. Little Flower purchases a natural indigo dye powder from south India and mixes it with hot water and caustic soda. The mixture is left to ferment for two days and then strained into lukewarm water to make a dye bath.
Once the dye has been prepared, artisans use a Japanese resist dyeing technique called shibori to create patterns on cotton fabric.
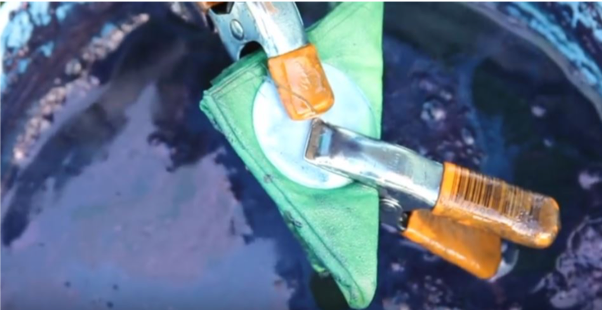
Itajime shibori is a form of shibori in which templates are used to block specific sections of the fabric from the dye to create a pattern. Once the template is securely in place, the fabric is soaked by hand in the dye bath. Once the fabric dries, the templates are removed. Each piece varies slightly, making each Indigo Geo Print Pillow and Shibori Scarf a one-of-a-kind work of art.
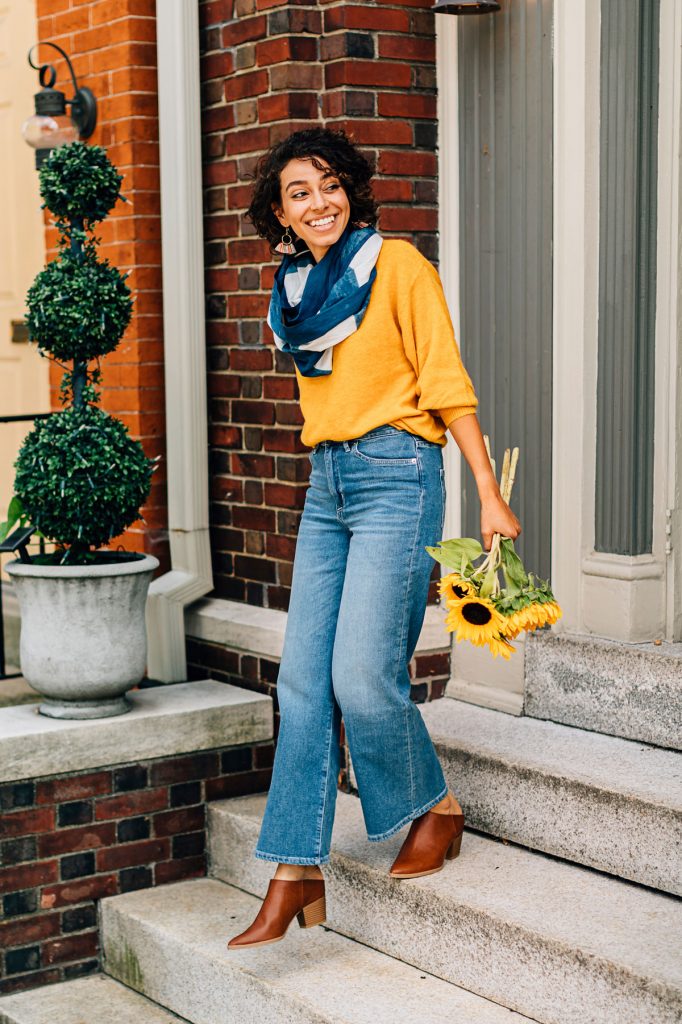
The shibori process used for the Indigo Robe crafted by dye artisans working with Manushi in Nepal is slightly different. The cotton fabric is laid on a flat surface, and a cotton rope is laid on top of the fabric.
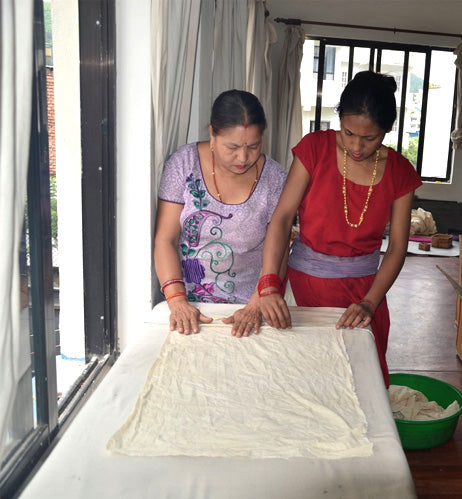
The fabric is then rolled tightly around the rope. The artisans squeeze the fabric toward the middle of the rope, scrunching it together from both ends.
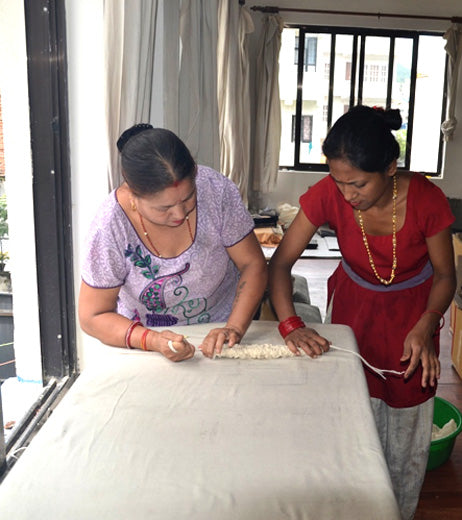
Next, the rope is tied to together at the ends, forming the rolled fabric into a small hoop.

The rope creates the resist dye pattern.
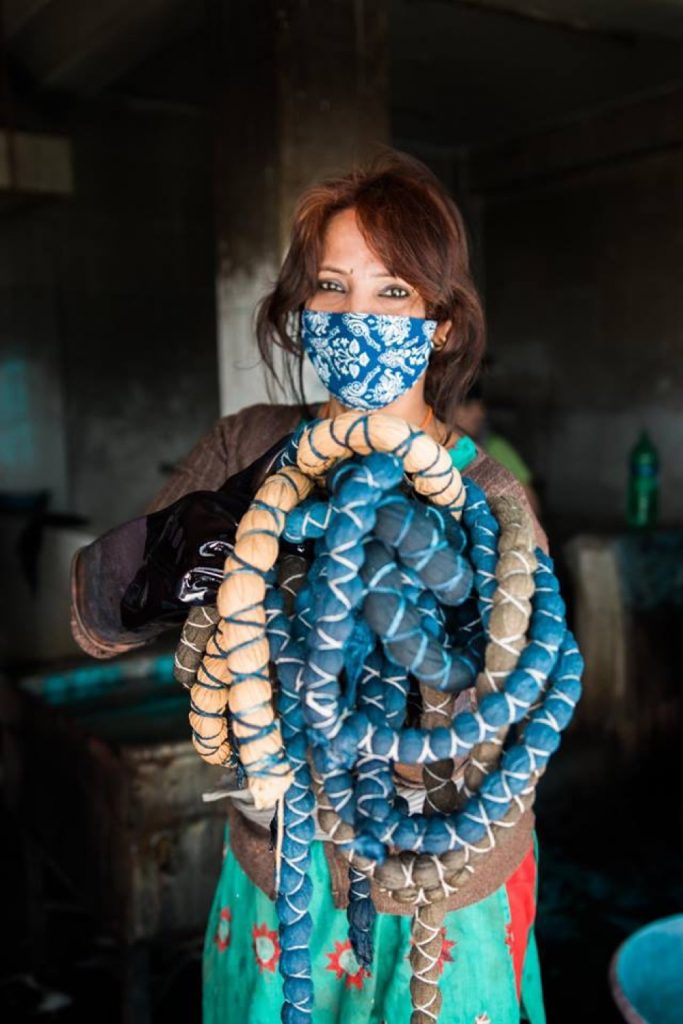
The fabric is soaked by hand in AZO-free indigo dye. Once the fabric has dried, the ropes are removed.
Anu Dwarika Shakya – Master Dye Artisan
The dye artisans of MESH and Manushi are valuing process and craftsmanship over expediency, and the difference is noteworthy. The Indigo Geo Print Pillows and the Indigo Robe may be a long time in the making, but it’s clear that they are well worth the wait.
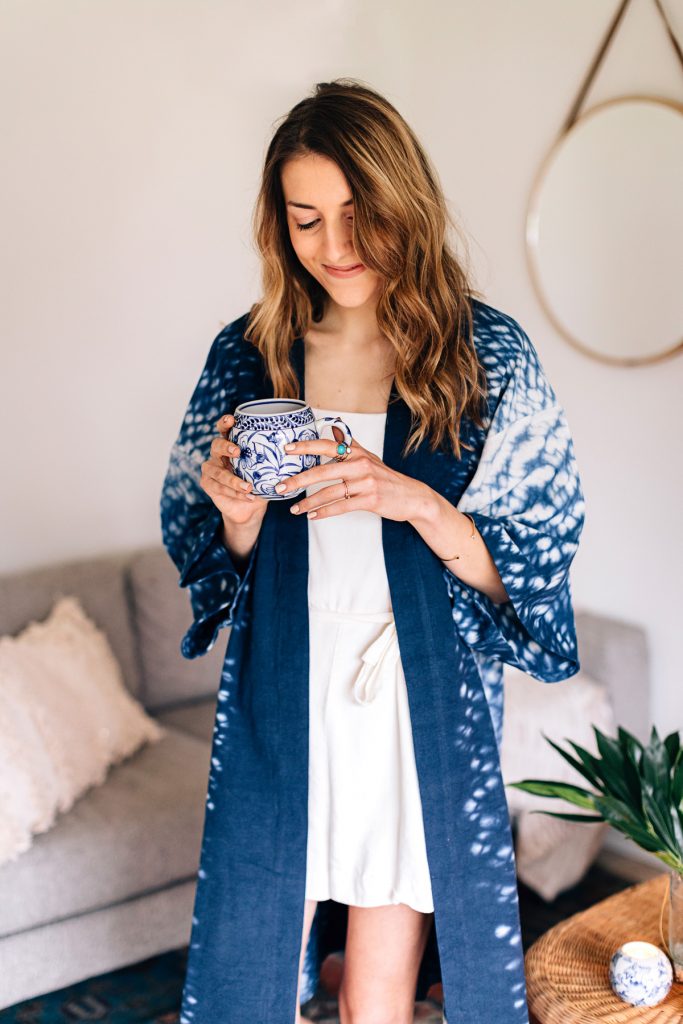
Leave a comment